La nuova valigia K5600 punta al rispetto dell’ambiente con la nuova gamma di bauletti dalla caratteristiche ben delineate: made in Italy, tecnopolimeri, la prima top di gamma del gruppo in materiale riciclabile.
Givi fa sempre più tendenza per motocicliste e motociclisti. Viaggiare in sicurezza e con tutto il comfort, nel rispetto del nostro pianeta, rinunciando al superfluo in nome di un’economia che mette al centro l’essere umano. Una soluzione sembra essere quella proposta da Kappamoto, il marchio di Givi SpA che esprime il meglio della ricerca e dell’esperienza dello storico Gruppo, fondato Giuseppe Visenzi, per rispondere agli appassionati del mondo delle due ruote dall’animo green.
ll Project Manager Elia Lombardi: “Ci guida un’etica ambientale di ispirazione umanistica. Siamo un’azienda italiana specializzata nella produzione di accessori in metallo, in plastica, in materiali compositi e sentiamo la responsabilità di agire nel miglior modo possibile”. Vediamo come si concretizzano questi buoni propositi.
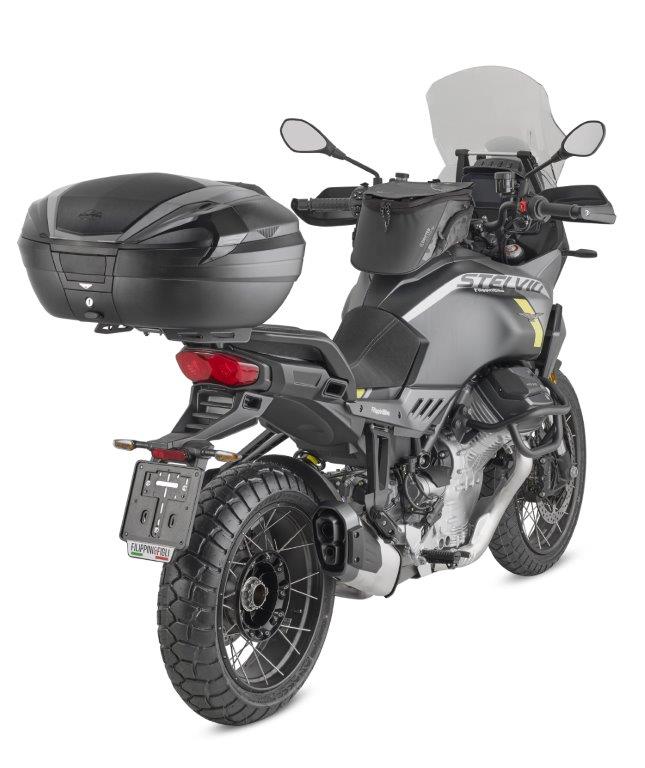
Givi: la nuova valigia K5600
La nuova valigia K5600 esprime bene questi valori delineandosi come top di gamma dei bauletti in plastica della marca: Made in Italy, in tecnopolimeri, la prima top di gamma del gruppo è in materiale riciclabile. La presentano il project manager Elia Lombardi, con Catia Leoni, responsabile della comunicazione, e designer delle borse morbide del Brand. Il nuovo top case K5600 costituisce una tappa significativa di un percorso che punta verso la completa sostenibilità che il marchio porta avanti da diversi anni.
Un’altra tappa fondamentale sono le borse Eco Rambler in Nylon riciclato, ‘etiche’ anche nei dettagli, con la fodera interna non tinta che riduce l’acqua utilizzata nei processi di tintura, per eliminare gli agenti inquinanti e ridurre il consumo energetico.
A seguire, la valigia K4900 è realizzata con il compound K’BLUEPLAST costituito da plastica riciclabile e una componente importante di plastica riciclata, che permette la riduzione di emissioni inquinanti e al tempo stesso offre ottime prestazioni meccaniche.
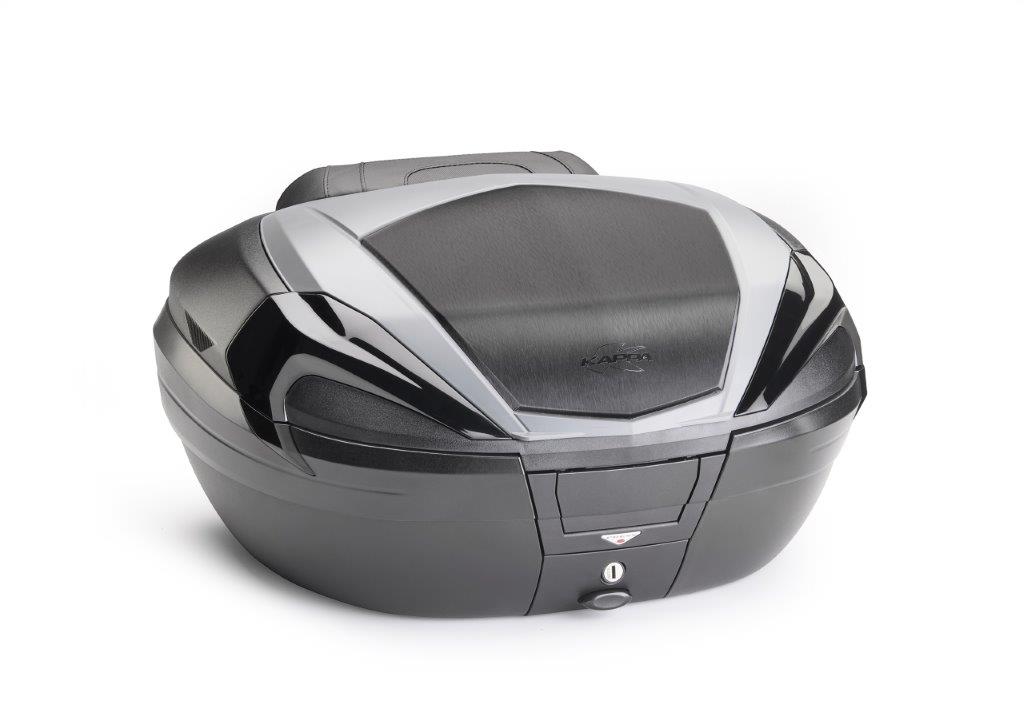
L’approccio green a Design e Utility si esprime ora anche nella K5600. Un prodotto realizzato senza l’impiego di verniciature, che renderebbe la plastica meno riciclabile. Sono stati ottimizzati e adattati vecchi stampi, si sono studiate strategie per semplificare e ridurre le fasi operative (e relativi costi) fino ad ottenere una raffinata reinterpretazione di un prodotto senza tempo con criteri di sostenibilità.
Spiega il project manager Elia Lombardi: ”L’obiettivo della sostenibilità nel nostro ufficio tecnico guida ogni attività, dalla ideazione allo studio di come si muovono le mani degli operai che devono costruire l’oggetto, fino alla fase dei test e alla presentazione. Veniamo da una formazione di design industriale che considera pedagogia e psicologia applicate al progetto e ci offre una visione più completa e umanistica dell’iter progettuale.
Per noi sostenibilità è prima di tutto rispetto dell’essere umano. Se per assemblare delle cinghie l’addetto deve sforzare le sue mani lavorando con fatica e insoddisfazione, creiamo un sistema per tenere aperte le nostre valigie in alluminio senza cinghie: è nata così l’idea della cerniera di rotazione dei coperchi “speciale”, utilizzata su tutta la gamma K’Mission che regge totalmente l’apertura dei coperchi ed evita il pericolo dell’effetto “ghigliottina” sulle mani dell’utilizzatore. Queste cerniere semplificano e rendono più a misura d’uomo sia le fasi produttive, sia l’utilizzo del prodotto evitando la chiusura accidentale del coperchio durante l’azione di carico e scarico.
Da considerare poi che un oggetto che non c’è, non si rompe e non deve essere riciclato. Meno stampi, meno energia consumata: Less is More! Ci rivolgiamo quindi a consumatori attenti a questi valori, pronti a sacrificare alcuni dettagli e funzioni superflui a vantaggio di un’estetica pulita ed essenziale, che comunque non rinuncia mai a stile, sicurezza, performance e praticità. Per noi è una sfida continua, ma creare prodotti con un’anima è anche una vera gioia!”.
Givi, come lavora l’azienda
GIVI produce internamente articoli e attrezzature complete in metallo, plastica e materiali compositi, coprendo l’intero ciclo industriale successivo alla materia prima, fino alla creazione di un accessorio per moto.
La maggior parte delle plastiche utilizzate è vergine, ma viene impiegato anche materiale riciclato, generato internamente. Ad esempio, il riciclato, viene utilizzato per scaldare le presse e avviare il ciclo di produzione. Inoltre, l’azienda lavora costantemente per ridurre gli scarti di trasformazione, ottenendo ottimi risultati nonostante l’altissimo rapporto tra varietà e numeri di serie.
GIVI è intervenuta anche sull’accessibilità delle informazioni e sull’assistenza ai clienti, un servizio di importanza fondamentale oggi, che comunica con clienti in tutto il mondo. Vengono riparati prodotti anche molto datati e ciò è possibile grazie alla progettazione accurata degli stessi.
Eliminata anche gran parte della carta per le istruzioni sui prodotti: sia i negozi sia gli utenti finali attraverso l’uso di QR code possono accedere sempre a informazioni aggiornate. L’azienda sta lavorando anche su contenuti extra-prodotto e sugli imballaggi. La ricerca è orientata a rendere gli accessori il più possibile riparabili, contrastando la tendenza dell’obsolescenza programmata che caratterizza gran parte della produzione industriale.
“Crediamo nel design circolare: è fondamentale pensare fin dall’inizio alla creazione di un oggetto destinato a durare, facilmente riparabile in tempi brevi e con modalità semplici. Tuttavia, ammettiamo che la strada verso una piena economia circolare è ancora lunga”, sottolinea Lombardi.
Un altro aspetto su cui si lavora è la semplicità di trasformazione e completamento degli articoli con accessori. Ad esempio, mentre gli schienali per i bauletti richiedono spesso di forare coperchi o fondi, lo schienalino K233S per la valigia KMS44 Mission utilizza fori e viti già presenti, che svolgono anche una funzione strutturale del prodotto.
“Questa semplificazione generale offre all’azienda l’opportunità di investire maggiormente nella ricerca, permettendole di proporre prodotti sempre migliori. Così, Kappa Moto si è affermata come marchio di accessori affidabili, durevoli e pratici per moto e scooter, costruendo una community di utilizzatori etici e altamente fidelizzati.” Un piccolo grande esercito di ‘rivoluzionari senza armi’, armati solo di intelligenza lungimirante e cuore.
Valigia MONOKEY® K’5600 completamente Made in Italy in sintesi
Top case con inserti in policarbonato nero lucido e finitura effetto alluminio spazzolato nero sulla cover centrale.
Sistema di aggancio: MONOKEY®, il sistema di fissaggio per bauletti e valigie moto più diffuso al mondo.
Caratteristiche:
• Chiusura Security Lock di serie
• Capacità: 56 litri, due caschi modulari
• Carico massimo: 10 kg
• Ambito utilizzo touring / urban
• Cover perimetrale grigio stampato in massa, verniciabile
• Materiali: Tecnopolimeri e acciaio.
Accessori opzionali:
• TK756 – Borsa interna con maniglie e cinghia tracolla.
• KS150 – Piastra in tecnopolimero colore nero per carico aggiuntivo
• K640 – Schienalino morbido rivestito in tessuto similpelle nero
• K9910N – Rete elastica portaoggetti
Costo al pubblico: 289,00 € (Prezzo Italia, iva compresa)